In the last decade, 3D printing has emerged as a popular option in the industrial and manufacturing sectors for its flexibility and affordability. But how does it compare to the tried and tested methods of traditional injection molding? Is 3D printing cheaper than injection molding? And when should you choose one over the other?
Tamarack has created your complete guide to 3D printing vs. injection molding, with answers to all of these questions and more.
Injection Molding
Let’s start by looking at the more traditional solution: custom injection molding. This method involves injecting molten material, often plastic, into a mold cavity, where it cools and solidifies to form the desired product. Injection molding boasts efficiency and precision, making it a go-to choice for mass production of identical parts. Its versatility extends to a wide range of materials, producing durable and high-quality items with consistent results.
3D Printing
On the other side, we have 3D printing, an innovative technology that has garnered widespread attention for its additive manufacturing process. 3D printing constructs objects layer by layer, translating digital designs into tangible prototypes or end-use products. It is popular for its customization capabilities, allowing for intricate and complex geometries that would be challenging to create with traditional methods. 3D printing is also popular because it can often be completed in-house, as long as you have a machine large enough for your project.
Injection Molding vs. 3D Printing: How to Choose
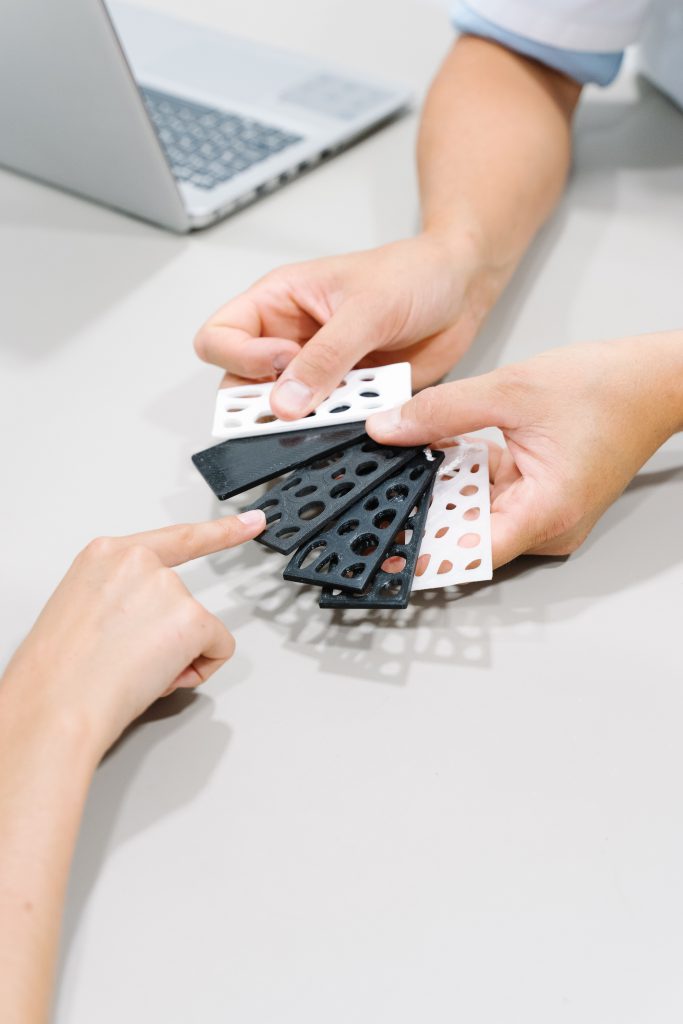
Project Type and Design Stage
Perhaps the biggest factor that will determine whether you should use 3D printing or injection molding is the type of project you’re working on and its stage of development.
3D printing can create a new part quickly—within hours or days of being designed—which can then be tested. Companies can easily produce a part, find flaws, and then quickly create a new iteration to test its improvements. Because of that, it’s a solid choice for rapid prototyping, one-off designs, and producing small batches of highly specialized components.
Meanwhile, plastic injection molding excels in large-scale production runs, churning out identical parts with high speed and efficiency. If you’re manufacturing thousands of units, injection molding is the way to go.
Therefore, many manufacturers can make great use of both technologies. They use 3D printing to test different parts and prototypes quickly and cheaply until they come up with a design they’re satisfied with. Once they’re finished, the designers can use the prototype as a basis to create a custom injection mold, which will allow them to create thousands of parts for the final product.
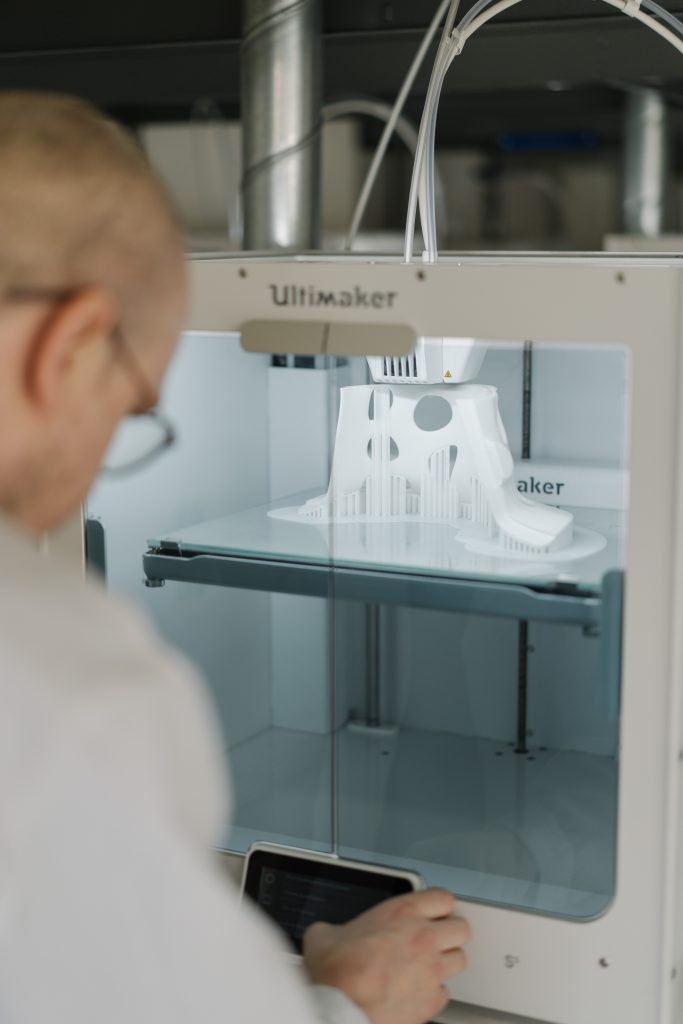
Speed and Quantity
Over the years, 3D printers have become progressively faster. While a 3D printer can create a new part in several hours, it will take several weeks to see the first finished part, usually identified as T1 testing, made from custom injection molding. That’s because the mold’s design needs to be checked for viability and quality before it is created. Once it is approved, the first prototype can be made and verified to ensure the client is happy before the manufacturer starts full production.
However, once production does begin, custom injection molding can create parts within a matter of seconds. Then the production speed of injection molding will quickly catch up to and far surpass 3D printing. So if you need parts in any kind of considerable quantity, injection molding is the better option.
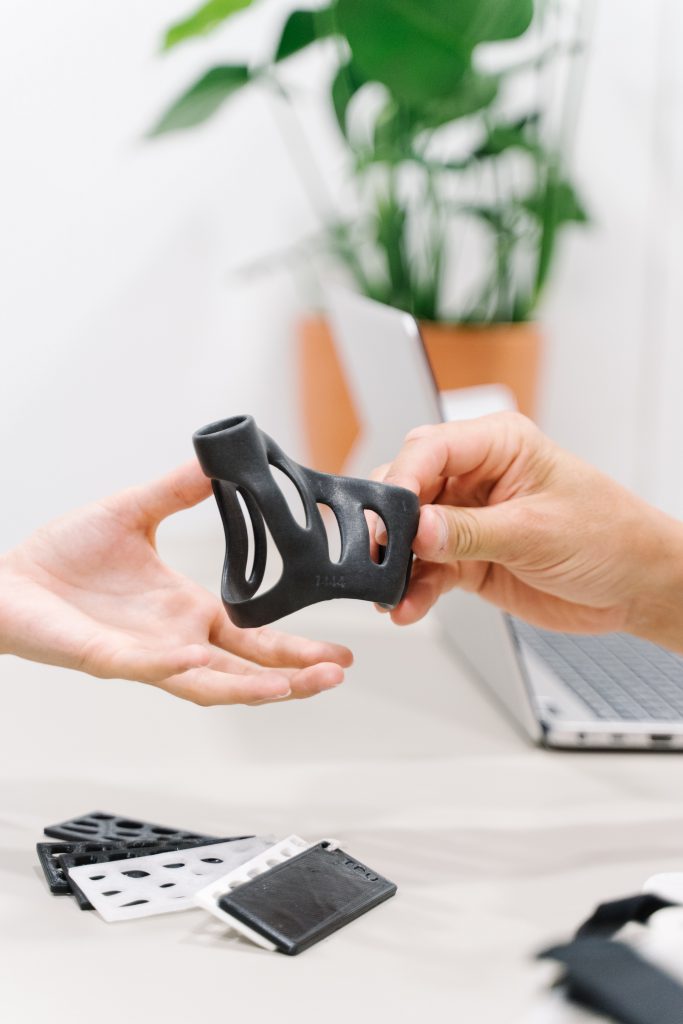
Cost
Just like with speed, comparing the cost of 3D printing vs. injection molding is dependent on the number of parts you need. The cost of a 3D printer can vary widely depending on the size, type of material, speed, accuracy, and precision of the device. You can find professional-grade 3D printers for several thousand dollars, however they can run up to $100,000. Once you have a printer, creating a part is relatively inexpensive; you just need to pay for the cost of materials.
Custom injection molding can also have a larger upfront cost that can vary widely depending on the type of part to be manufactured. The size, complexity, and output quantity will all be factors in the cost of creating your parts. However, as a rule of thumb, the more parts you order, the lower the per-unit cost is likely to be.

Strength
While strength may not be the objective during the design and prototyping phase, the durability of your part is of crucial importance when it goes into use. 3D printed parts have come a long way in terms of strength and durability as the printers and the materials they can work with have improved. However, they still aren’t a match for custom-injected molding.
Parts made with injection molding have been used in virtually every industry for their reliability and durability. It remains the method of choice for manufacturers that anticipate any kind of wear and tear on their products.
Custom Injection Molding with Tamarack
If you’ve decided that you’re ready for custom injection molding for your project, Tamarack Industries is ready to help. Our injection molding services can handle intricate and complex products anywhere from 1 gram and 2,267 grams. The molding presses we use can exert between 25 and 500 tons of clamping force to create a high-quality finished product.
Tamarack also offers fully-featured services for secondary operations, including ultrasonic welding, drilling, and the assembly of your parts.
Tell Us About Your Project
Ready to start creating parts using custom injection molding? Reach out to Tamarack’s experienced team and tell us about your project.