If you’re planning a custom injection molding project, one of the first things you’ll want to determine is cost. Whether you’re developing a small run of prototypes or mass-producing thousands of parts, there are several factors that will affect this. Understanding these can help you plan more effectively and ensure you get the best value for your investment.
Custom Injection Molding Cost Factors
Tooling
One of the first and most significant expenses in custom injection molding is the tooling—the creation of the molds used to form your parts.
- Design complexity: More intricate designs require more precise molds, which can increase costs. If your part has complex geometries, tight tolerances, or undercuts, the tooling process will take more time and effort which will lead to higher costs.
- Material for the mold: The material selected for the mold itself also impacts pricing. Molds made from hardened steel are more durable and can withstand high-volume production but are more expensive to manufacture. Aluminum molds are cheaper but less durable, which makes them better suited for prototyping.
- Precision and manufacturing: The precision needed during the tooling phase is another key cost factor. The more accurate the mold, the better the final product will be, but achieving that level of precision requires advanced technology and highly skilled labor.
- Durability and reusability: While tooling may represent a significant upfront cost, the long-term savings can be significant if you plan to produce a high volume of parts. A well-made mold can be used repeatedly, which reduces per-part costs over time.
Material
The type of material used in injection molding will play a big role in determining the cost of the project. Different materials have varying properties, such as flexibility, temperature resistance, and durability, all of which can impact pricing. Material selection is critical to balancing performance needs and cost, so it’s important to work with your injection molding partner to select the material that meets your needs without inflating your budget.
- Thermoplastics: These are the most commonly used materials in injection molding due to their versatility and relatively low cost. Common types include polypropylene, polyethylene, and ABS. These materials are often chosen for their durability and ability to be recycled, which can also lower long-term costs.
- Resins: Resins are often selected for more specialized applications, such as automotive or medical components. High-performance resins offer excellent strength and resistance to heat or chemicals, but they come at a higher cost than standard thermoplastics.
- Specialty Polymers: For highly specialized applications, specialty polymers might be required. These materials are designed for unique performance characteristics like high UV resistance, electrical insulation, or extreme flexibility. However, these specialized materials can also come with a premium price.
Production Volume
One of the key ways to lower the cost per part is through high production volumes. Injection molding is particularly cost-effective when producing large quantities because the significant upfront costs, such as tooling, are spread over more parts. With smaller batches or prototypes, the cost per part will be higher because the tooling and setup costs aren’t offset by a high number of units.
Part Complexity
Another factor that can dramatically affect the cost is the complexity of the part design. The more intricate the details of your part, the more challenging the mold will be to produce and the longer the cycle time for each part. Working with an experienced injection molding partner can help optimize your design to reduce costs while maintaining the necessary functionality.
Parts with tiny, intricate features may require specialized molds, which can drive up the tooling cost. These features can also lead to longer cycle times, further increasing production costs. Also, if your part is composed of multiple components that need to be molded together, this adds another layer of complexity and cost. Each additional component increases both tooling and production time.
Additional Service and Post-Processing
In some cases, your injection molding project may require additional services or post-processing steps, which can add to the overall cost.
- Ultrasonic welding: This service may be necessary to join plastic parts together without the use of adhesives or fasteners. While it creates a seamless finish, it introduces an extra step in production.
- Drilling: For some designs, precise holes or openings may need to be added after initial production. This step requires specialized equipment and can extend production time, impacting the overall cost.
- Assembly: If your project involves multiple parts that need to be assembled, this process can increase labor costs and overall production time.
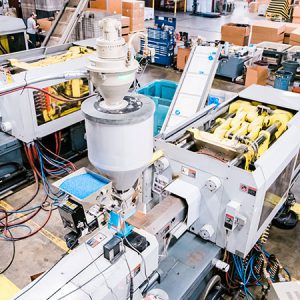
How Long Does Injection Molding Take?
In addition to cost, another important consideration for custom injection molding projects is the timeline. Injection molding timelines can vary based on whether you need a mold created from scratch or if you’re using an existing mold.
If you need a custom mold made, the process can take several months, especially if the mold is being produced overseas. The timeline includes design, tooling, and trial production runs to ensure the mold is ready for full-scale production.
However, if you already have a mold, the process is significantly faster. You simply need to send the mold to the injection molding company, and they can begin production almost immediately. Depending on the project, this can reduce the timeline to just a few weeks.
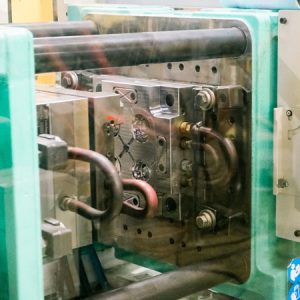
Custom Injection Molding from Tamarack
Tamarack Industries offers high-quality injection molding at competitive prices. Not only are we able to handle complex designs, but we also have a wide-ranging shot capacity—anywhere from 1 to 2,267 grams. Our molding presses have 25 to more than 500 tons of clamping force, and we offer a full range of support services, including ultrasonic welding, drilling, and assembly.
Get a Quote on Injection Molding
If you’re ready to start or need a more accurate estimate based on your specific needs, contact Tamarack for a quote. Our team will help you navigate the complexities of the process, from design to material selection, and provide transparent pricing to ensure you stay within budget.